You face a choice every day on the shop floor when you chase flexibility and speed or lean on deep planning and buffer stock.
In Industrial Engineering: Lean Vs Traditional Manufacturing, you will discover which approach drives your costs down without crippling delivery.
In this Lean vs Traditional Manufacturing comparison I will cover:
- Core goals and real gains of each method
- How waste, inventory and change play out in Lean vs Traditional Manufacuring
- Practical steps to test and blend both in your operation
Keep reading for clear examples and action items you can try this week.
Why Industrial Engineering Matters to You
You manage machines, people and deadlines. You need systems that hum, not stall.
Industrial engineering gives you proven frameworks to spot hidden delays, cut defects and balance cost with quality.
I remember walking a floor where late shifts stacked pallets of parts nobody ordered.
The team spent hours clearing space and losing revenue.
We mapped every step, found three unneeded handoffs and saved 15 hours of work that week.
You can start small.
Grab your process map, ask “Where do I wait most?” and dig in.
For a broader view of your role, read What Is Industrial Engineering and Why Is It Important?.
That guide lays out how engineers shape every link in your chain.
Lessons from History: Where It All Began
You tap into a century of insight. In the early 1900s, engineers like Frank Gilbreth timed every motion to cut wasted movement.
They proved small savings add up to big gains.
Those early studies birthed tools you use today.
Time-and-motion work led to 5S and Kaizen.
Forecast-based planning grew from Frederick Taylor’s experiments in mass production.
Each step in that history offers tactics you can revive.
Dive into The History of Industrial Engineering to trace how simple observations turned into the lean and traditional models you rely on.
You will spot methods to adapt for your changeovers or batch runs.
Lean Manufacturing Deep Dive
Lean strips out every step that fails to add value. You build only what your customer needs, exactly when they need it.
Core lean moves:
- Map each process step with your team
- Hunt non-value activities (waiting, overproduction, defects)
- Empower every person to suggest quick fixes
At an electronics shop I consulted, swapping circuit boards cost 12 minutes each time.
We installed quick-change kits and cut that to two minutes that freeing 40 production hours monthly.
The picture below show how organise workplace can also increase productivity
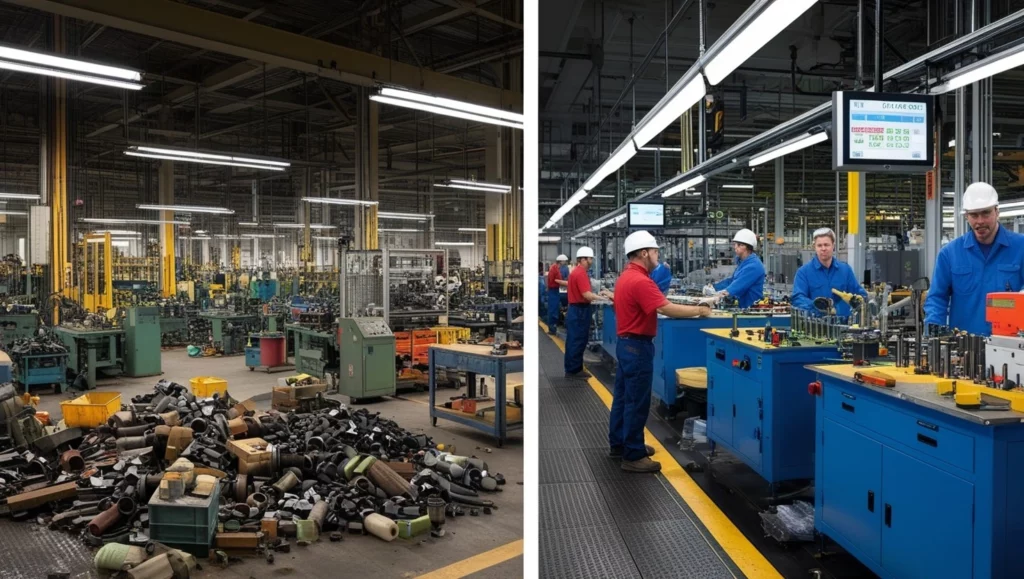
Try tools like 5S for workstation order, Kaizen events for rapid fixes, Kanban boards that pull parts on demand and poka-yoke fixtures that stop errors.
Automate mapping and metrics with platforms listed at industrial engineering software tools.
Traditional Manufacturing Unpacked
Traditional methods lean on forecasts and batch runs. You plan weeks or months ahead, run large batches and hold safety stock to meet peaks.
Core traditional steps:
- Forecast demand based on past data
- Schedule large, steady production runs
- Keep buffer inventory to dodge shortages
At a chemical plant, reactors cost $10,000 to restart. They ran 72-hour cycles, stored extra product in tanks and saved $15,000 each avoided shutdown.
Traditional suits processes where stops hurt more than storage, steel mills, glass furnaces, continuous chemical reactors.
You trade warehouse space for uptime and volume discounts.
Side-by-Side Comparison
Factor | Lean | Traditional |
---|---|---|
Inventory | Low | High |
Batch size | Small, frequent | Large, infrequent |
Planning horizon | Days to weeks | Months |
Changeover cost | Low (quick change) | High (long setups) |
Response to change | Fast | Slow |
Storage investment | Minimal | Significant |
Stockout risk | Higher (if unchecked) | Lower (with buffer) |
You spot where each approach fits. Lean cuts storage but demands discipline. Traditional buys uptime at the cost of cash and space.
Navigating Your Choice
You don’t have to pick one method exclusively. Many teams blend lean and traditional where each makes sense.
Ask yourself:
- How stable is your demand?
- Which packs a bigger punch: frequent changeovers or high storage costs?
- Do you need instant quality feedback or can you absorb delays?
Answering these steers you to lean cells, traditional runs or a hybrid layout. You might pilot lean in final assembly and keep batch runs in forging or molding.
Where Lean Manufacting Wins
Lean excels when orders shift and lead times tighten. You slashed storage, boosted flow and improved quality.
Look at areas like:
- Automotive sub-assembly with multiple variants
- Electronics lines where products switch each shift
- Hospital labs where test volumes spike unpredictably
Pilot lean in one cell. Track lead time and defect rates for four weeks. If you cut lead time by 20 percent or more, you have earned the green light to scale.
Where Traditional Manufacturing Shines
Traditional shines when stopping costs outpace storage. You keep lines running, machines humming and tanks full.
Ideal candidates:
- Steel plants and glass furnaces with long heat-up cycles
- Chemical reactors that need days to reach process temperature
- Food or beverage lines tuned for large batch yields
You load once, run long and leverage volume discounts. You accept extra inventory as the price of uninterrupted output.
Combining Lean and Traditinal Approaches
You can blend both methods for best results.
Example mix:
- Apply lean in final assembly, where product mix shifts fast
- Stick to traditional batch runs in forging, casting or molding
Run a lean pilot in assembly. Measure floor space, inventory turns and defect rates.
Compare those metrics to the rest of your plant before expanding.
This hybrid model delivers flexibility where you need it and stability where you can’t afford stops.
Your Action Plan
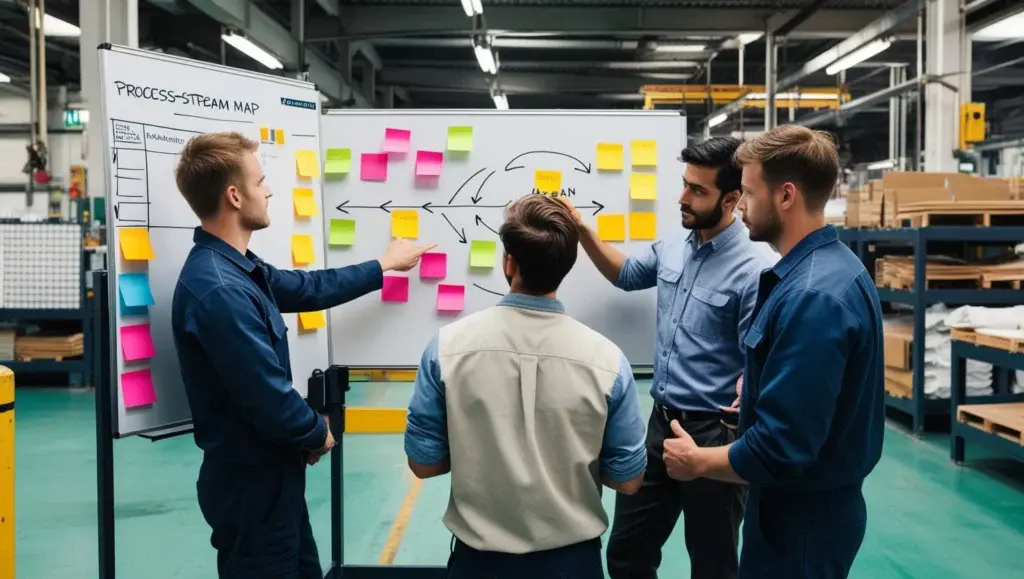
- Map your process end-to-end. Capture every step from raw input to finished goods.
- List three wastes you can remove this month—overproduction, waiting or defects.
- Host a half-day Kaizen event with your frontline staff.
- Track lead time and defect rates weekly using simple forms or dedicated software.
- Review data. Decide where to expand lean and where to keep traditional buffers.
Automate mapping and data collection with tools at industrial engineering software tools.
Industrial Engineering: Lean Vs Traditional Manufacturing- Final Thought
You have explored both sides of Industrial Engineering: Lean Vs Traditional Manufacturing.
You have seen how lean strips waste and speeds flow, and how traditional buffers deliver uninterrupted runs.
You have traced each method back to its roots and mapped out clear steps to pilot and measure results on your floor.
This is not theory your next action will prove what works in your operation.
You hold the power to test, measure and refine.
You can blend approaches to cut costs, boost quality and hit delivery targets.
Which strategy will you pilot first and what metric will you use to prove its success?
Let me know in the comments below.
If you love what you read here please support me with any donation to Paypal:franckchanda@gmail.com it helps with research and maintaining this website.
I really appreciate any help you can provide.